Disperse Dyes Dyeing Method
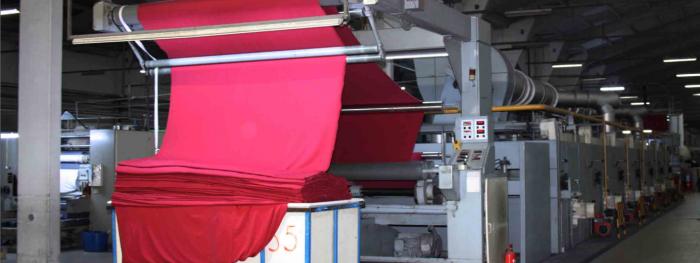
1. High temperature high pressure dyeing
Polyester and its cotton blends dyeing:
Pretreatment:
Pretreatment of PC or PV is a must before starting the dyeing operation.The pretreatment is essential to remove the lubricant oils and other auxilairies used during spinning and weaving or knitting operations. Thefollowing simple treatment is enough to remove those impurities.1.
Recipe:
Lissopal D paste = 2 grams/liter
Soda Ash = 2 grams/liter
Treat with the above recipe at 90~95°C for 20 minutes.
2. Drain - Hot Wash @ 70°C for 10 minutes - Cold wash - Neutralize with 1cc/liter Acetic Acid.
3. Check the pH - 5.5 to 6.
Dyeing Process:
Polyester textiles require a Heat Setting operation before dyeing. Heatsetting eliminates the internal tensions within the fiber generated duringmanufacture and the new state can be fixed by rapid cooling. This heatsetting fixes the fabrics in the relaxed state and thus avoids subsequentshrinkage or creasing of fabric.
Dyebath Setting & dyeing:
Set up the dyebath with the following auxilaries and chemicals:
● Lyogen DFT = 0.5 gpl
● Sandozen PES = 1.0 gpl
● Acetic Acid = 1 gpl
● Check pH to 5.5 to 6.0
- Set the dyebath with the above materials. Raise the temperature to50°C and run for 10 minutes
.- Dissolve the dyestuff with soft water at 50°C and filter it.
- Add the dyestuff slowly in to the bath. Check the pH to 5.5. to 6
.- Raise the temperature to 115°C at 2°C per minute and run 10 minutes.
- Raise the temperature further from 115°C t0 135°C at 0.5°C per minute
.- Hold for 45 to 60 minutes according to the depth of the shade.
- Lower the temperature to 80°C and drain the bath.
- Do Hot Wash (70°C) for 10 minutes followed by cold wash.
Reduction Clearing:
This is the process to improve the fastness of the dyed material by removing all thedyestuff that is superficially adhearing to the fabric and staining the cotton portion of the blend. The following method is found to be most suitable for any depth of dyeing.
Recipe:
Cyclonon ECO = 2 gpl
Acetic Acid = 2 gpl
Treat the fabric at 70°C for 20 minutes. Do hot wash and cold wash. Drain andunload the batch.
Dyeing process for nylon, triacetate,polyester and acrylic fibers.
At A set bath at 50° A - Add Auxiliaries & Acetic Acid At
At B add Disperse Dyes (pre-dispersed
2. Carrier dyeing
Carrier dyeing is carried out under atmosphere pressure by an addition of carrier tothe dyeing liquor. Methylnaphthalene or chlorobenzene type carrier is usedgenerally, which is added in concentration of 2-7 g/L to the dyeing liquor.
Other conditions of the dyeing liquor are the same as those for high temperaturedyeing. The temperature is raised gradually from 40-60°C and continued for 90-120min at 100°C.
In carrier dyeing, in some case the troubles such as tarring of dye or carrier spot aretaken from the no stability of emulsifier in the carrier under high temperature or someother conditions. Therefore, it is necessary to select the carrier so as to prevent thetroubles.
Reduction cleaning as stated in high temperature high pressure dyeing.
3. Thermosol dyeing
Thermosol dyeing is a continuous dyeing method which is applied mainly for thepolyester/cotton blended materials. General dyeing condition is as follows.
Dye and 0.5-2g/L of migration inhibiter (for example, sodium alginate) and alsowetting agent if necessary are added to the padding liquor.
Squeezing is carried out 1dip 1 nip at room temperature, pick up 65-70%. Drying at70-90_C.
After padding and intermediate drying, thermosol fixation is carried out by dryheating for 60-120 sec. at 180- 210°C depending on the form of the material andtype of disperse dyes.
- E type: 180-190°C x 60-120 sec
- SE type: 180-200°C x 60-120 sec
- S type: 200-210°C x 60-120 sec
Reduction cleaning as stated in high temperature high pressure dyeing.